Decarbonizzare la produzione
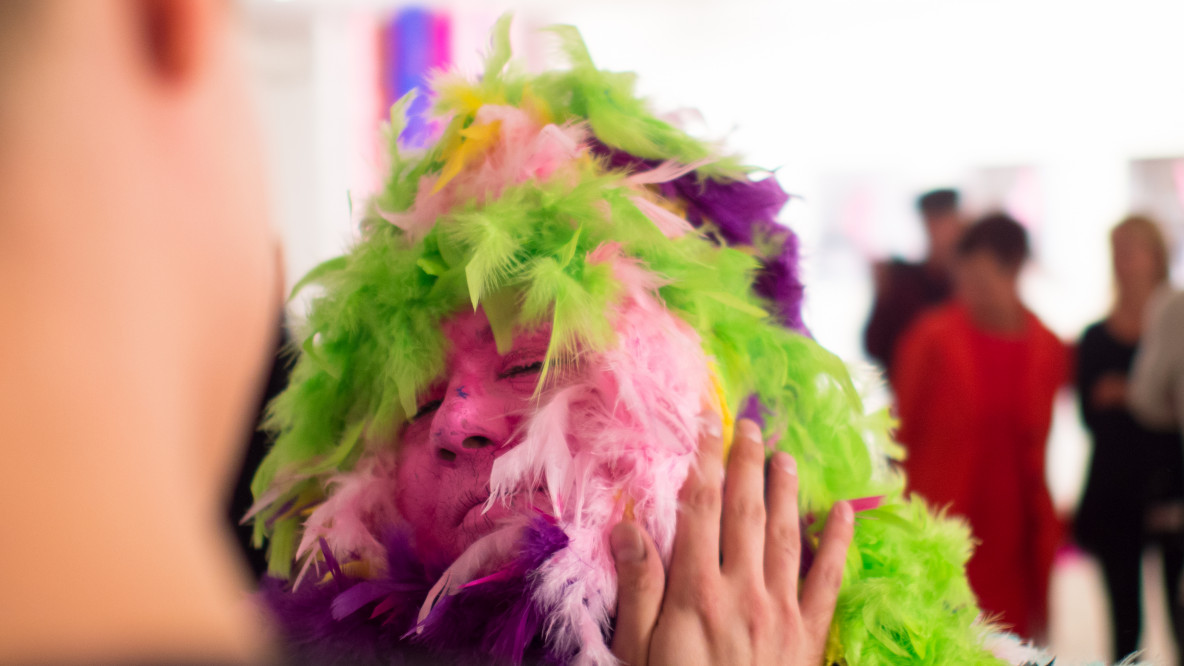
Con uno studio di fattibilità le aziende della rete Automotive Excellence Südtirol si propongono di sviluppare un monitoraggio standardizzato in tempo reale dell'impronta di CO₂ utilizzando digitalizzazione, sensori e soluzioni Internet of Things (IoT). Un altro passo per aumentare la sostenibilità delle imprese del NOI Techpark di Brunico, il nuovo hub che ha aperto i battenti a maggio 2023. La quantità di anidride carbonica che emettono i processi produttivi e i prodotti necessita infatti di una risposta sempre più urgente, soprattutto per le attività che si trovano a competere a livello internazionale. Questo vale anche per i più importanti fornitori dell'industria automobilistica dell'Alto Adige, che si sono uniti nella rete di innovazione Automotive Excellence Südtirol (AES). Ed è anche importante per i clienti, afferma Wolfgang Knollseisen, direttore finanziario di Alupress. L'azienda di Bressanone, specializzata nel settore dei componenti in alluminio pressofuso pronti per il montaggio, è capofila del progetto Live Carbon Footprint, che consiste nel registrare e monitorare l'impronta di CO₂ dei processi produttivi e dei prodotti.
Dall'impronta di carbonio stimata a quella effettiva
«Il campo della rilevazione e della quantificazione dell'impronta di carbonio dei prodotti e dei processi produttivi non è di per sé nuovo. Da tempo esistono metodi e strumenti per la cosiddetta valutazione del ciclo di vita, o LCA (life cycle assessment)», spiega Erwin Rauch, che con la sua cattedra “convenzionata” nel settore della produzione intelligente e sostenibile sarà uno dei responsabili scientifici di unibz nel nuovo NOI Techpark di Brunico. Tuttavia, queste tecnologie non sono ancora sufficientemente diffuse né applicate in modo generalizzato nelle aziende.
Come primo passo, nell'ambito del progetto Live Carbon Footprint, le aziende intendono sviluppare uno standard che permetta di identificare l'impronta di CO₂ dei prodotti “from cradle to gate” (“dalla culla al cancello”), cioè dall'estrazione delle materie prime alla fornitura del prodotto finito al cancello della fabbrica, nel contesto delle gare d'appalto. «Lavorando insieme agli altri fornitori altoatesini del settore automobilistico, possiamo condividere le nostre esperienze e arrivare a definire uno standard comune», afferma Knollseisen, direttore finanziario di Alupress. Ma non solo. In una seconda fase è necessario confrontare l’impronta effettiva del prodotto con il valore calcolato in precedenza. In futuro questo dovrebbe essere fatto attraverso il live tracking, cioè la registrazione continua dei dati rilevanti e l'osservazione dell'andamento del PCF nel tempo.
«Il potenziale principale del progetto risiede nella possibilità di calcolare l'impronta di carbonio di un prodotto e successivamente elaborare i dati in modo sistematico e metodologicamente corretto. Per questo ci supporta Fraunhofer Italia. Al termine dello studio di fattibilità valuteremo se le singole aziende hanno i prerequisiti necessari a questo scopo o capiremo cosa sarà necessario fare in futuro. La prospettiva a medio termine sarebbe quella di sviluppare congiuntamente uno strumento di monitoraggio dell'impronta di carbonio in un successivo progetto di ricerca e sviluppo e di attuarlo nelle aziende AES», afferma Rauch.
Questo monitoraggio in real time è auspicato dall'azienda produttrice di materie plastiche Intercable, partner di progetto, perchè le permetterebbe di effettuare rilevazioni dirette sia in fase di produzione che di offerta di nuovi progetti e di allineare la pianificazione in base all'impronta di CO₂.
Un ulteriore vantaggio che vede il partner di progetto Tratter Engineering, un altro produttore di componenti in plastica, risiede nell'estrazione delle materie prime e nella riduzione delle immense distanze di trasporto. «Il nostro processo più dispendioso dal punto di vista energetico è senza dubbio la tempra dei pezzi», afferma poi Michaela Golser di GKN Driveline. Da tre anni è in corso la conversione del processo di tempra. In un nuovo impianto, invece di impiegare il gas usato finora, si lavorerà con l'elettricità che in GKN è al 100% ecologica grazie all'energia idroelettrica.
GKN Sinter Metals vuole realizzare un domani prodotti a zero emissioni di CO₂,e la partecipazione a questo progetto è una delle strategie per raggiungere questo ambizioso obiettivo. Tra le altre azioni, l'azienda di Brunico punta a ulteriori investimenti nella digitalizzazione dei propri processi, nell'efficienza delle risorse e negli acquisti sostenibili e nell'integrazione dei dipendenti.
In definitiva, la ricerca nel campo della produzione sostenibile presso la nuova sede del NOI Techpark di Brunico parte da un livello elevato con un ampio bagaglio di esperienze e competenze delle aziende locali, che continuerà a crescere grazie al nuovo progetto comune. «Lavorando insieme, da un lato creeremo una piattaforma per lo scambio di idee per favorire il risparmio e l'ottimizzazione dell’energia, dall'altro svilupperemo congiuntamente sistemi che potranno essere adottati anche da altri settori», conclude il responsabile del progetto Wolfgang Knollseisen.
Di produzione intelligente e sostenibile si parlerà anche al Forum Internazionale Meccatronica il 28 e il 29 settembre al NOI Techpark di Brunico. Chi ha interesse a partecipare si può iscrivere entro il 15 settembre. Qui un assaggio del programma:
Visite in aziende: GKN Automotive, Intercable e GKN Hydrogen a Brunico; Durst Group a Bressanone; Loacker Konfekt, Heinfels, Tirolo Orientale
Relazioni di speaker internazionali come Manfred Ruhmer (Infineon) e Markus Siegert (Siemens)
Due sessioni parallele di interventi sul tema "Produzione intelligente e sostenibile: soluzioni di meccatronica per il futuro":
Sessione A – Sustainable Manufacturing
Sessione B – Sustainable Mobility
Stimme zu, um die Kommentare zu lesen - oder auch selbst zu kommentieren. Du kannst Deine Zustimmung jederzeit wieder zurücknehmen.